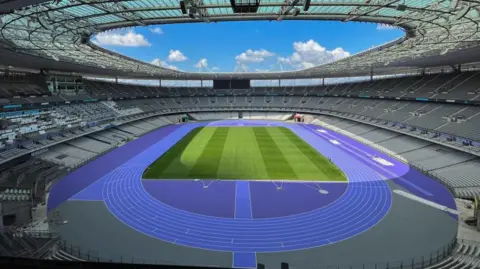
Could the Paris Olympics track be the fastest ever made?
To the casual observer one athletics track probably looks much like another.
But when the Olympic Games open in Paris on Friday, it will be difficult to miss the purple track at the Stade de France.
Describing its colour as “audacious”, Maurizio Stroppiana, whose company made the track, says it will help people “instantly recognise” the Paris Games.
It took 10 wet and cold weeks to lay the track at the Stade de France after the Rugby World Cup ended in October of last year.
“Finally, when we see it installed, it’s absolutely beautiful,” says Mr Stroppiana, whose Mondo Group, based in the Italian town of Alba, has made every Olympic track since 1976.
The company, named after its founder Edmondo Stroppiana, began making rubber bicycle tyres in post-war Italy, moving into tracks in 1972.
It says the Paris track is its fastest yet, 2% faster than Tokyo’s in 2020.
Beneath the purple lies a rubber track with two layers. The lower level has honeycomb cells, where air absorbs the shock of your foot landing, then pushes out, feeding the energy back as your foot takes off.
Mondo
The lower level of the Paris track has honeycomb structure
Tracks have come a long way since Sir Roger Bannister ran the first sub-four-minute mile at the University of Oxford’s Iffley Road facility in 1954.
That record was set on a cinder track, considered the best surface at the time.
Sir Roger, who was president of the Oxford University Athletics Club, organised the new track to replace its bumpy predecessor.
“He decided a new 440-yard (402m) cinder track had to be built,” says his son Thurston Bannister.
Cinders are volcanic rocks riddled with gas bubbles. To form the surface of a running track they were mixed with clay, peat moss, or ashes from burning coal, which held the surface together.
They gradually replaced dirt, grass, and wood running surfaces in the mid-nineteenth century.
Cinder tracks were harder and faster, but they had one big disadvantage.
“You would be covered in dirt if it was any way wet or damp. It was always fun to see yourself at the end of a session,” recalls Maria McCambridge, who competed in the 5,000 metres at the 2004 Athens Olympics.
Getty Images
Sir Roger Bannister was running on a cinder track when he broke the four-minute mile in 1954
The Olympics used red cinder until 1968 and the Mexico City games, which instead featured a polyurethane “Tartan” track, so-called because 3M, which made it, also made Scotch tape.
Though not necessarily faster, these tracks held up better in the rain. With cinder tracks, rain often cancelled athletics competitions.
Polyurethanes are man-made polymers – big molecules made of lots of repeated units.
They are still used today in athletics tracks, but have seen much improvement according to Shaun Goudie, head of Sports Group, which makes sports surfaces, including athletics tracks, for big sporting events.
“The different polymers we have today can be tailored specifically to certain things like spike resistance and ultraviolet light resistance,” he says.
Getty Images
The 1968 Mexico City Games were the first Olympics to use a polyurethane track
The 1976 Montreal Olympics, was the first to use a rubber track from Mondo.
“We had a fabulous Mondo track at the Athens Olympics. I like the hardness of them. I definitely feel that they are a lot faster than tartan tracks,” says Ms McCambridge.
However that hardness could cause problems. “Some distance runners would often complain of very tight calves for a few days after racing,” she says.
“Participants in the 10,000 metres would often be seen wearing racing flats over spikes for that reason,” she remembers.
Reuters
Track materials can be tweaked to help direct more of the athlete’s energy forward
“A track has to have contradictory properties. So the ideal track has to be both hard and soft,” notes João Bomfim, a polymer chemist in Luxembourg who previously headed research and development for Mondo.
The harder the surface is, the faster you can run. “You can run quicker on concrete or asphalt than sand on the beach,” he says.
But you also hit a track with a force three times your body weight, so that force needs to be “absorbed or at least not returned at all once,” he says.
The idea is that the impact helps you move forward instead of causing injury.
Using two layers of rubber, and choosing different components in making each, lets you include contradictory characteristics, says Mr Bomfim.
Using different additives when preparing the rubber allows the track designer to “fine tune more energy absorption or more elastic recovery,” he says.
Today’s highest-performance tracks can be made using either polyurethane or rubber, says Tadhg Sullivan from Ireland’s Dundrum South Dublin Athletics Club, which installed a rubber Mondo track in 2022.
He explains that one big difference between the two surfaces is the way they are installed. Polyurethane tracks are mixed on site, while rubber surfaces are made in pieces at a factory, and then assembled into a track on the site.
This, he says, makes rubber tracks a bit easier to install in countries that get a lot of rain – like Ireland.
Steward Humble
Anika Schwarze-Chintapatla is looking forward to training on Oxford’s new track
Oxford is now installing a new polyurethane surface at Iffley, where Sir Roger set that record 70 years ago. It is made by German firm Stockmeier.
Anika Schwarze-Chintapatla, a steeplechase runner, studying medicine at Trinity College, Oxford, is looking forward to the new track after training on less forgiving surfaces gave her stress fractures.
“I’m really excited about the new track, and injury being less of a worry,” she says.
It will also be dark blue, the university’s colour.
Running is “such a mental, psychological game: there’s definitely something there with the visuals, the colours,” she adds.
“The only easy colour for rubber is black, that’s the colour for tyres,” observes Mr Bomfim.
“Any rubber that is not black will be a challenge. One that is almost impossible is white,” he notes.
Much of the development in tracks from the late 1990s to the present day has involved making them more environmentally friendly.
First, by removing asbestos and sulphur and then by using renewable materials.
The track in Paris is made up of 50% recycled materials, says Mr Stroppiana.
Other green tracks are on the market. Sports Group has the Rekortan brand, which has a surface made from a polyurethane derived from canola and rapeseed oils.
So whether red or purple, the future of athletics tracks is likely to be a shade of green.
More Technology of Business
Source link : https://www.bbc.com/news/articles/crg4d5vn0n0o
Author :
Publish date : 2024-07-22 23:06:50
Copyright for syndicated content belongs to the linked Source.